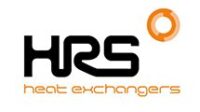
Opinion piece
The benefits of ‘drying’ biogas
You normally associate drying and water removal in anaerobic digestion with digestate management and the reduction of water volumes to improve digestate management. However the biogas generated contains a mixture of compounds alongside methane, including water vapour. While this is removed by those plants exporting biomethane to the gas grid or for other uses, such as a transport fuel, it is not always considered by those burning biogas in a combine heat and power (CHP) facility.
With subsidies for renewable electricity generation dwindling, it is more crucial than ever that each part of the AD process is optimised. Not only that, but if water enters a CHP engine it can decrease its efficiency and lead to corrosion, resulting in reduced biogas yields and engine damage. CHP engines are one of the most expensive pieces of equipment to replace on an AD plant, so it makes sense to look after them. Additionally, an inefficient CHP engine will result in lower electrical output and higher capex, and therefore reduced profits – a 1 MW digester operating at even 80 per cent capacity could be losing as much as £16,000 each month.
As well as improving efficiency and longevity of gas engines, removing water from the biogas prevents corrosion of other pipework and components, and removing the water also removes a proportion of water soluble gases such as hydrogen sulphide, ammonia and siloxanes. It can also increase the life of activated carbon and other filters and less water in the engine’s fuel means less contamination of lubricating oil.
Existing methods to remove water from biogas include condensate traps and ‘air conditioning’ type chillers, but these are not designed to produce low enough temperatures and so are either operated outside of their design parameters, or they don’t remove enough water to prevent all of the issues mentioned above.
The HRS Biogas Dehumidification System (BDS) is specifically aimed to prevent such issues, with the minimum use of additional energy. Rather than heating the biogas to dry it, the BDS uses condensation to remove water from the gas, and also includes a heat recovery section to further increase overall plant energy efficiency.
By reducing biogas temperatures from around 40oC to approximately 5-7oC, more than 90 per cent of the water volume is condensed out of the gas. A chiller system supplies coolant which is transferred to heat exchangers: biogas flows on the product side of the exchanger, while the coolant flows on the service side. As the biogas cools, the water condenses from the gas, leaving a clean and dry biogas ideal for use in CHP engines. The heat recovery element means that the cold biogas is used to pre-cool any incoming biogas before entering the CHP. This reduces the load on the final cooling heat exchanger and recovers as much as 20 per cent of the energy needed for the process.
– ENDS –
Notes to Editors
Photos
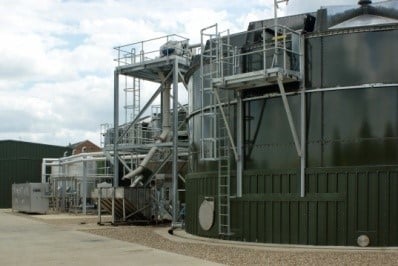
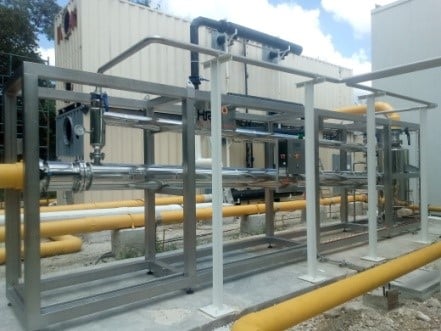
About HRS Heat Exchangers
Located in the UK, HRS Heat Exchangers is part of the HRS Group which operates at the forefront of thermal technology, offering innovative heat transfer solutions worldwide across a diverse range of industries. With almost 40 years’ experience in the energy sector, specialising in the design and manufacture of an extensive range of turnkey systems and components, incorporating our corrugated tubular and scraped surface heat exchanger technology, HRS units are compliant with global design and industry standards. HRS has a network of offices throughout the world: Australia, New Zealand, UK, Spain, USA, Malaysia and India; with manufacturing plants in the UK, India and Spain.
For UK media enquiries about HRS Heat Exchangers, please contact:
Yenni Maelianawati, Senior Marketing Manager, HRS House, 10-12 Caxton Way, Watford Business Park, Watford, Herts. WD18 8JY
Tel: 01923 232 335
Direct Email: yenni@uk.hrs-he.com
Email for publications: info@uk.hrs-he.com
www.hrs-heatexchangers.com
Release issued by GloHouse Media: Bev Small, bev.small@glohouse.co.uk, Tel: 01223 872239 / 07901 841491
Our Ref.: hrs-ex-181105-c-en