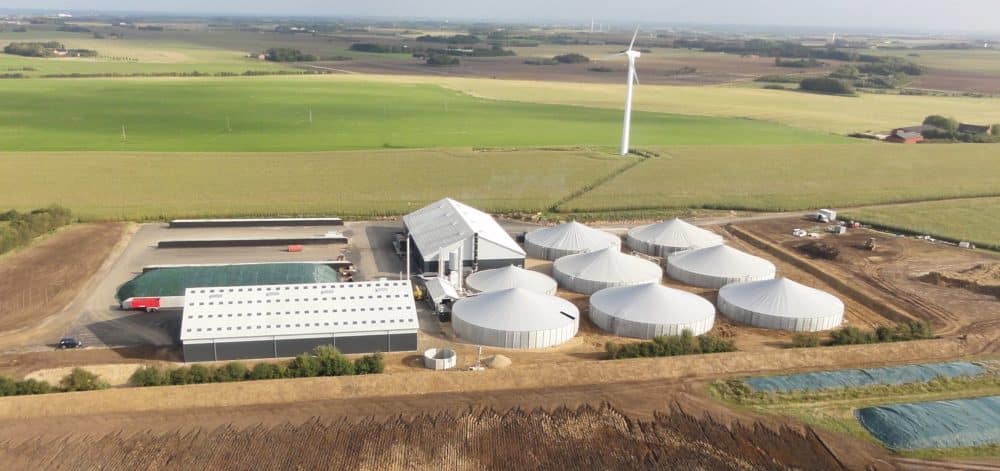
7. Case study 2 – Boe Madsen / Madsen Bioenergi
The farming brothers left reeling by the 2008 crash who saw the future was in fuels
Boe Madsen and his two brothers established their 150,000 tonne per annum biogas plant in 2014, using organic wastes supplied by farms within a 10km radius. But their journey began in 2008 in response to the global financial crash.
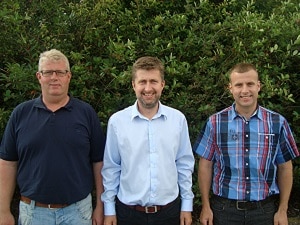
The three brothers were farmers, two ran pigs and a the third grew crops and vegetables, but none were getting a secure and reasonable return from their land. Two of the brothers were supplementing their incomes working as mechanical engineers. The crash and associated volatility in the commodity market made them want to find a more stable income. They hit upon biogas.
Boe recalls, ‘Commodity prices were fluctuating, and banks were put off by the margins in agriculture. We needed to produce something where the business is bigger. We saw the future is in fuels, especially as the government also stated manure had to be degassed and the nitrogen in manures should be used.’
Planning and development started in 2011 but was initially hard to fund due to the ongoing banking crisis. The plant cost DKK 65m (roughly £6.5m). However, because they were adopting innovative new systems (see below) they received capital funding of DKK 11m from the government. The Danish government routinely offers capital support to green energy projects that are pursuing innovative models to improve efficiency – all part of its commitment to remain a world leader in green energy tech.
Madsen Bioenergi was one of 19 successful projects out of 67 that applied for funding. Once that was in place it was easier to raise funds from banks and venture capital. Funding was secured on a forecast output of 400m3 per hour; today they are delivering 600m3 per hour.
The three brothers operate the site full time. Boe says, ‘You have to focus on biogas as a living or just don’t do it! It requires the same amount of effort as a 600 head herd of cattle or 2,000 sows.’
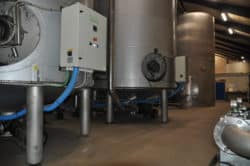
They operate to exacting standards. The site is spotless, and they make great efforts to sweat the small stuff. They routinely check the production line twice a day and immediately act if they see anything not quite right. For instance, they have drip trays beneath all operational machinery. If they see a drop of fluid, they immediately investigate. ‘We don’t want to be woken in the night by the alarm, so we address the issue then before it becomes a big problem.’
Throughout the site the brothers take a belt and braces approach. The site requires two compressors at full production. Three are installed so one can be serviced without disrupting production. They use a wood burner for process heat but have a gas back-up rigged up, too. They operate this systematic approach along the process.
They upgrade the biomethane through an Ammongas amine upgrading system. “It would be very stupid to produce electricity. Denmark can store 1 billion m3 of gas, 3 months’ supply, that is a big battery. Upgrading is the future, biomethanation. In 2-5 years’ time we’ll use the CO2 and take all the energy from seven nearby wind turbines to deliver high energy and fuels for planes.’
This will either happen on site or through a centralised biomethanation plant in Skive.
Plant | Skive, Denmark |
Commissioned | 2014 |
Owner & Operator | Owned and operated by Boe Madsen and his two brothers.
· The brothers have stopped farming, acknowledging that to do biogas right requires their full attention. · Routine checks across the site are undertaken twice a day, to keep the site tidy and spot early warning signs of potential issues. ‘A drop of oil represents a potential issue that is best addressed before it becomes a cause for alarm.’ |
Feedstock | 400 tonnes per day (tpd); 380 t liquid (manure) feedstock, 40 t processing/commercial waste, 15 t of FYM (straw-based manure), 45 tpd of energy crops, and glycerol irregularly. |
Output | · 600 m3/hr biomethane to grid (no propane required)
· 140,000 tonnes per annum (tpa) of natural fertiliser · 3 on-site operators and one full time driver. · 20 farms within a 10km radius supply manure, which is collected, processed and returned |
Financials (Estimates) | · DKK 65m (£8m) for the plant. DKK 11m was secured as capital funding, (that was provided to 19 plants with progressive business models out of the 67 that applied), and the rest was 50% venture capital and 50% bank loans.
· DKK 35m (£4.2m) gas-to-grid sales per annum · DKK 3m to lay 11km of pipe work to the gas grid. This was a more cost-effective solution than making a connection closer to the facility, which would have required the biogas to be delivered at higher pressure and propanation. |
Process | Feedstock and Digestate
· Feedstocks from liquid reception, farmyard manures and the on-site external clamps are all mixed in an underground tank housed beneath the reception building, which makes stone removal simple as they can be removed following them settling that prevents them from entering the multiple digesters · The feedstock is passed through a heat exchanger, using heat from the upgrader to increase the substrate temperature to 50℃, which is then pasteurised using the Ammongas upgrading systems surplus heat. · Fed into the 6 tanks with a total digester volume capacity of 31,500m3. · The digestate goes through a separator. The liquid fraction is stored and the separated fibre is recirculated, pumped back to the start of the process for another HRT (hydraulic retention time) of 70 days as not all the straw has been fully digested. Gas and Heat · The raw biogas does not need treating before entering the absorber. The impurities are removed from the biogas and dissolved into the amine. · CH4 rich biogas is passed through a carbon filter to remove the remaining H2S (5-0ppm), compressed, cooled and dried before being analysed for grid entry. · The amine solution is heated to remove the impurities. This heat is provided by a separately housed straw and waste wood biomass burner. · The upgrading system also provides around 1MWh of surplus heating for process and feedstock heating and pasteurisation. · 100% of the gas is upgraded and injected into the grid, as there is no CHP or biogas used on-site. |
Interesting Factors | · Operators
· The three brothers are all from a farming background. Two had pig farms and the third a vegetable farm. Two of the brothers are trained mechanics/technicians. · Feedstock o They cover the transport costs of feedstock collection and digestate delivery and pay farmers up to DKK 3 for good muck with a high fraction of dry matter (DM). Farmers pay for muck with a low DM fraction to be treated. o Use a contractor with a mobile hammermill for their FYM feedstock. · Control Room · This is kept air conditioned to 20℃ for the electrical systems. · Upgrading o They use a waste wood and straw-fed biomass boiler to heat the upgrader – with a natural gas boiler on standby as contingency. o 5 hours of maintenance per annum on the upgrader. o 3 compressors working on site, with one spare to allow for maintenance without requiring downtime. · Public Engagement o Keeping it Danish: Grid initially questioned the use of Ammongas upgrading as only two reference plants at the time. Ammongas’ upgraders are now the most common in Denmark. o Actively engaged with the 12,000 local citizens regarding traffic and odour concerns. All feedstock and digestate operations (unloading and loading) are undertaken in a closed reception facility. o Currently taking further steps to improve the odour abatement system. The current system cost 2m DK and has meant they have not received one complaint. Following improvements, it will include a biofilter extraction unit to capture the manure odours displaced as tankers refill with digestate. · Budget o Currently 12% energy crops allowed but this will drop to 6% in 2021, to meet the sustainability targets of the subsidy regime. o Their budget was based on 400m3 per hour; they are delivering 600m3 per hour. |
You must be logged in to view the rest of the content on this page.
To request a login and password, contact us at info@worldbiogasassociation.org
If you have login details, please enter them below.