
10. Ammongas Amine Upgrading for biogas
Over the past five years since it entered the biogas market, Ammongas’ amine upgrading system has become the most widely deployed upgrading technology in Denmark. The system has been installed on 20 facilities in Denmark – and counting – and is now making inroads across Europe.
The upgrading technique uses amine to separate the CO2 and H2S from the biogas to deliver biomethane, using a very low parasitic load of 0.1kWh/m3 of biogas. The system uses lower pressures compared with those that employ more traditional upgrading solutions, as compression comes after the upgrading has taken place, meaning only the biomethane is upgrade (see below for full tech spec).
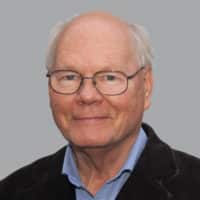
“We’re different from our competitors, as in our system we don’t need to compress to high pressure,” says Anker Jacobsen, founder and owner of Ammongas. “Most need to compress methane and CO2, we just need to compress the methane so our demand for compression is low.”
Where Ammongas has service agreements the system achieves a conversion rate of over 99%, essentially delivering more biomethane at less cost.
It was Mr Jacobsen who instigated our trip to Denmark, to see first-hand how the industry is developing. As a career development engineer his catchphrase is ‘there has to be a better way’.
Biogas replacing natural gas is one of those ways. “Biogas does a lot of very good things,” says Anker. “By taking the organic fraction and making biogas, we are helping the whole of society, preventing the release of climate change emissions and reducing air pollution and creating thousands of jobs. With it, the vision of a greener world is one step closer.”
Technology | Ammongas Amine Upgrading |
Applications | Ammongas’ amine raw biogas upgrading technology to produce grid quality biomethane and for the removal of impurities is the most widely deployed upgrading technology in Denmark. The gas sweetening principle is taken from proven technology in the oil and gas industry. |
Maintenance | 24/7 monitoring is provided to operators who enter service agreements with Ammongas, which has developed a network of technicians across the country, reducing downtime to a minimum, calculated in hours rather than days. |
Advantages and Lessons Learnt | · Spare heat can be used for pasteurisation and feedstock heating. The Madsen BioEnergi site (600m3/hr of biomethane to grid) upgrading system provides 1MW of heat from the upgrading system.
· Spare compressor on-site and 24/7 support to reduce downtime. · Amine has a greater selectivity towards CO2/CH4 separation and has a better loading capacity than water, which leads to smaller liquid recycling streams and lower pressures. o Lower pressure means scaling up of plants does not have a large price tag added, as the system has the capacity to cope with increased throughput. · Amine has reduced electricity demand (0.1kWh/m3 biogas) due to lower pressures than water scrubbing. · Ammongas continually researches their amine solutions to identify the right pressure and heat, and use an amine solution that requires the least pressure. · Compression comes after upgrading meaning only biomethane is compressed, which reduces the compressor size and hardware and electrical consumption costs. · Methane loss is below 0.04%. |
Downstream Processes | 1. Raw biogas from the digesters/fermenters is passed through the CO2 absorber column, with a watery solution of alkaline liquid (1/3 amine and 2/3 water) that dissolves and removes the acidic pollutants in the gas (CO2, H2S and more).
a. The CH4 rich gas is released from the column (1) then requires conditioning. i. Initially to passes through activated carbon to remove the low levels of H2S still present. ii. The CH4 rich gas is then compressed, cooled, dried and analysed before being injected into the grid as biomethane, which has a purity in excess of 99%. 2. The CO2 is absorbed into the amine (catalyst) without the use of pressure, because of the chemical process. 3. The saturated amine solution is heated in the CO2 stripper column, with water, to remove CO2, H2O and H2S, which regenerates the scrubber liquid. a. In a reflux system, steam, H2S and CO2 are separated with the water returned to the system following condensation. b. The CO2 and H2S are then passed through a H2S filter before the CO2 is released. CO2 can be captured at this stage. 4. Automatic ‘topping up’ of amine solution occurs due to only a small (0.00004 L amine/m3 biogas) amount being lost in the saturated CO2. 5. Excess heat is taken from the process’s absorber, compression and reflux system (circa 85℃) stages that can then be provided to the AD process for heating of feedstocks, digesters, and pasteurisation, or space heating of offices and buildings. The heat can be delivered at >85℃ or 45℃. |
You must be logged in to view the rest of the content on this page.
To request a login and password, contact us at info@worldbiogasassociation.org
If you have login details, please enter them below.