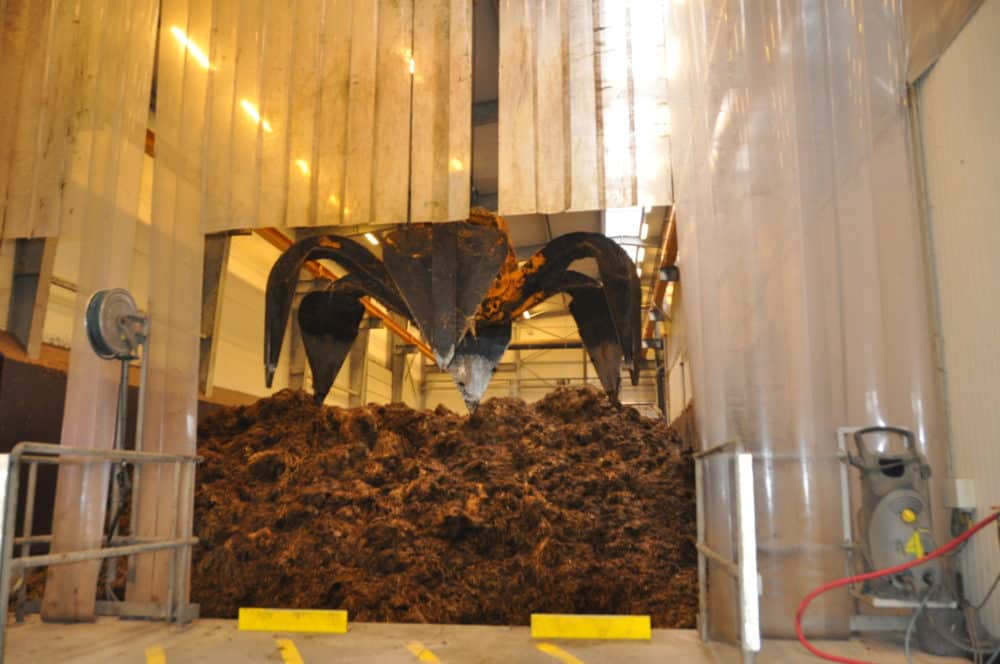
11. Tech Focus
During our visit we were taken by two bits of kit; the integrated process for feedstock unloading and digestate loading, and the automated feedstock crane, both of which served to make the operation of the plant more efficient.
The feedstock/digestate drop and go technology.
1: Tanker arrives and enters enclosed warehouse. 2: Offloads feedstock and uploads digestate. 3: Note the offload and onload nozzles are at an angle to each other to facilitate a more efficient change and connection. The tanker leaves having been pressure hosed down. The whole operation takes around 10 minutes. The tech is commonplace on most facilities.
Technology | Adjacent feedstock and digestate delivery and collection, using a controlled crane arm. |
Applications | Delivering liquid feedstock and collecting digestate. |
Maintenance | Daily checks of valve operations and pipe integrity. |
Advantages and Lessons Learnt | · Reduced operator involvement of using manual bauer couplings and traffic movements on site.
· Tankers are positioned under an air filtration system inside the reception hall to reduce odour issues from displaced air during the feedstock-digestate exchange, installed as part of the agreements with local communities to obtain planning permission. · The process requires one air filtration system with reduced pipework requirements due to the integration of collection and delivery. |
Downstream Processes | Feedstock is stored in a tank and used for either direct pumping to fermenters/digesters or mixing with high DM feedstocks to increase pumpability.
Digestate is removed from site and delivered to on-farm storage for land application. |
The Automated Feedstock Crane
Feedstock is delivered and claw swings into action to move to back of reception area 3: Claw responds to demand for feedstock and delivers to the hammermill.
Technology | Automated feedstock crane |
Applications | Used to feed high DM FYM into the X-Hopper, and for managing the reception chamber. |
Advantages and Lessons Learnt | · Minimal operator involvement, such as loading feed hoppers, which reduces labour and human error, thanks to ‘smart’ (digital) communication with the hammermill.
· Automatically creates space in the reception hall by moving manures away from the unloading bays. |
Downstream Processes | The ‘muck claw’ is the first interaction with high DM feedstocks once they have been unloaded into the reception hall. The claw moves the manure to the back of the hall unless the hammermill automatically calls for re-loading.
High DM manures (FYM) post hammermill is mixed with slurry that has been heated using heat exchangers with excess heat from the biogas upgrading system. Once, mixed the substrate is pumped into the fermenters. |
You must be logged in to view the rest of the content on this page.
To request a login and password, contact us at info@worldbiogasassociation.org
If you have login details, please enter them below.