
6. Case study 1: Axel Månsson
Revenue stability and natural fertiliser – the reasons why Denmark’s largest producer of organic vegetables and eggs developed a biogas plant
Axel Månsson is first and foremost a farmer and a hugely successful one. He started out growing potatoes as a teenager on two hectares of land. Today his farm covers 1,400ha, producing over 30m pieces of vegetables and home to over 200,000 free range laying hens.
To get an idea of the scale of the operation the farm undertakes its own packaging across a vast array of warehousing and garages over 90 John Deere tractors and associated equipment and employs a full time team of five mechanics to keep them in good working order. The Månsson brand is ubiquitous across Denmark.
In 2011, however, it was delivered a body blow as a specialist producer of ice-berg lettuces. A food scare emerged in Germany which caused a crisis of confidence amongst consumers.
Germany experienced a major outbreak of VTEC, a form of e. coli, which caused HUS, a blood disorder that can result in kidney failure. A total of 908 cases of HUS and 3,168 cases of VTEC were reported, with 53 deaths attributed to the outbreak.
While fenugreek shoots produced from Egyptian fenugreek seeds were eventually identified as the most likely source of the outbreak, during the epidemic suspicion fell on other food products as possible sources of the infection, including tomatoes, cucumbers, and lettuces.
These suspicions, along with warnings from the authorities, led to a de facto ban on the import of Spanish cucumbers and to major economic losses of up to 80% of sales for a few German businesses. Danish cucumber and lettuce producers were also affected – mainly due to consumers’ reaction to the suspicion.
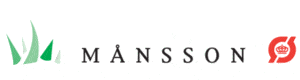
It was then that Månsson determined to diversify into biogas, to buffer the farm against such events and to regularise the inherent volatility of commodity markets and prices year on year. The other primary driver for him was the supply of digestate/biofertiliser this would deliver.
As a producer of vegetables, he was aware of growing consumer demand for organic produce, but there had to be a business case.
‘We use the money where it makes sense; when you can supply yourself with organic manure it’s circular and I always liked that. It made inherent sense to me to produce organically, I always thought it must be better if you can produce without chemical inputs.’
More than the consideration of sustainability is the need to earn money. ‘So, you learn slowly. You cannot change overnight. You have to learn to do it the best way before you change.’ Over half of the farm now delivers organically grown produce.
As he has hundreds of acres turned over to test beds for developing produce, so he determined to test biogas. ‘You learn slowly. You cannot change overnight. You have to learn to do it the best way before you change.’
His plant was built in 2014, to treat around 150,000 tonnes of organic wastes a year. It is currently being expanded to three times its original size.
Månsson doesn’t run the plant. ‘I didn’t want to leave the fields,’ he explains. So, it was developed with a forerunner of what is now Nature Energy, as equal partners. Nature Energy is responsible for operating the facility allowing Månsson to pursue his passion for farming.
Plant | Jutland, Denmark |
Commissioned | 2017 |
Owner & Operator | Owned in partnership by the farmer, Axel Månsson, and operated by Nature Energy. |
Feedstock | · 150 tpd (tonnes per day) that consists of: 100 t liquid (manure) feedstock, 20 t FYM (straw-based manure), and 30 tpd of energy crops and/or vegetable residues.
· 10% of the total feedstock comes from Månsson’s vegetable and layer (chicken) operations. |
Output | · 750 m3/hr biomethane to grid (no propane required) expanding to 1,900 m3/hr biomethane to grid.
· 150,000 tpa of natural fertiliser. · 4 on-site operators. · 50 farms in a 25km radius supply manure, which is collected, processed and returned as digestate. |
Financials (Estimates) | · £15m (DKK 126,000,000) for the original biogas plant.
· £15m for the plant expansion. · If manure feedstocks have a low N content, they pay for treatment. If the N content is high, they are paid. · Do not use biomethane or biogas to provide heat for the upgrader or process, as he can sell gas for DKK 6 and it costs DKK 2 to buy from the grid. |
Interesting Factors | · Axel Månsson moved into biogas to develop a steady income stream, as a counterbalance to volatile farming incomes.
· The plant is currently undergoing an extension to triple its feedstock inputs to 450 tpd. · Månsson did not want to operate the plant, recognising it would be time-consuming and require expertise. To allow him to continue farming he partnered with Nature Energy. · Månsson started farming at 15 with 2ha of potatoes and now has a cultivated area of 1,400 ha with 201,000 layers. |
You must be logged in to view the rest of the content on this page.
To request a login and password, contact us at info@worldbiogasassociation.org
If you have login details, please enter them below.