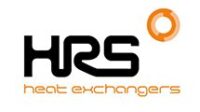
Member press release – Ireland biogas growth must focus on efficiency

By Matt Hale, International Sales & Marketing Director, HRS Heat Exchangers
Recent comments by ADBA chairman Chris Hunhe and Irish environment minister Eamon Ryan are positive for the expansion of renewable, green biogas production across the island of Ireland, but to maximise the benefits of increased anaerobic digestion capacity, operating efficiency and the use of digestate must be fully considered.
Speaking at a recent Joint Oireachtas Committee meeting on energy security and energy prices, Mr Ryan stressed the importance of biogas to the Republic’s energy plans, with a target of 5.8 TWh of energy from biomethane and anaerobic digestion, being produced from a mixture of grass, food waste and slurry.
Mr Ryan said, “If I recall correctly, that could involve up to 210 anaerobic digestion sites. That could provide about 15% of our gas needs and would give us some security. Anaerobic digestion has huge benefit potential for Irish farming because it gives a diverse and separate income and builds on what we are good at, which is growing grass.”
Meanwhile, at a recent event in Belfast, Chris Hunhe commented, “Northern Ireland is the best placed part of the UK to produce the most biogas and biomethane. It has the potential to meet 80% of its gas demand from this home-grown, cost-effective, and sustainable source thanks to the importance of livestock farming.”
HRS welcomes this ambition to increase biogas production capacity on both sides of the border, but to maximise the greenhouse gas savings from these plants, it is important to also maximise the efficient use of the high quality digestate biofertiliser produced during the AD process, as well as maximising biogas production.
HRS Heat Exchangers provides two systems specifically aimed at improving the efficiency of digestate production and maximising its value in both nutritional and economic terms.
Digestate Concentration

The HRS DCS uses patented technology to remove up to 80% of the water contained in the liquid fraction and concentrates it to 20% dry solids while, at the same time, maximising the nutrient content, using heat from the AD plant’s CHP engine. Less water also means reduced road and field traffic, bringing further benefits in terms of reduced compaction caused by the application of the digestate to land. The DCS is virtually self-sufficient – minimal energy or water is bought in, nothing is wasted, and the surplus energy from the CHP is re-used up to four times.
Another benefit of the DCS is odour control, which helps increase the nutrient content of the digestate. The high temperatures needed to concentrate digestate can cause the release of ammonia, largely responsible for the odours associated with digestate. However, the DCS overcomes this by acid-dosing the digestate with sulphuric acid, thereby decreasing the pH levels. This turns the ammonia into ammonium sulphate, which is not only less odorous, but is also an ideal nutrient.
Digestate Pasteurisation

To prevent the spread of potential pathogens which may be present in wastewater, either the feedstock or the digestate should be treated appropriately, with pasteurisation being a tried and tested technique. One of the most energy-, and therefore cost-efficient methods to pasteurise digestate is the HRS Digestate Pasteurisation System (DPS), which is based on heat exchangers rather than tanks with heating jackets. Using heat exchangers means that effective digestate pasteurisation is possible using surplus heat while allowing additional thermal regeneration levels of up to 60%. This saved heat can then be used for other processes, such as evaporation of the digestate to remove water.
The DPS and DCS are examples of several systems that HRS produce to improve the efficiency and sustainability of biogas plants and the anaerobic digestion process, with other examples including systems to dry biogas and recover waste heat from exhaust systems. Making biogas plants across the island of Ireland as efficient as possible will not only increase the environmental benefits they provide but will also improve economic returns for developers and operators, helping to increase the deployment of this vital technology.
– End –
About HRS Heat Exchangers
Located in the UK, HRS Heat Exchangers is part of the EIL Group (Exchanger Industries Limited) which operates at the forefront of thermal technology. HRS offers innovative heat transfer solutions worldwide across a diverse range of industries. With 40 years’ experience in the anaerobic digestion and biogas sector, specialising in the design and manufacture of an extensive range of turnkey systems and components, incorporating our corrugated tubular and scraped surface heat exchanger technology, HRS products are compliant with global design and industry standards. HRS has a network of offices throughout the world: Australia, Canada, New Zealand, UK, Spain, USA, Malaysia and India; with manufacturing plants in the UK, India, Spain and Canada.
For UK media enquiries about HRS Heat Exchangers please contact:
Yenni Maelianawati, Senior Marketing Manager,
3 Abloy House, Hatters Lane, Watford, Hertfordshire, WD18 8AJ
Tel: 01923 232 335
Direct Email: yenni@uk.hrs-he.com
Email for publications: info@uk.hrs-he.com
www.hrs-heatexchangers.com
Release issued by GloHouse Media:
Bev Small, bev.small@glohouse.co.uk, Tel: 01223 872239 / 07901 841491