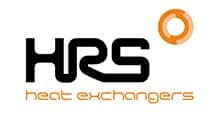
Member press release – The future potential of process control systems
By Matt Hale, International Sales & Marketing Director, HRS Heat Exchangers
Thanks to developments such as Industry 4.0, digitisation, and the cloud, together with improvements in process control and communication technology, it is easier than ever for equipment manufacturers to offer remote assistance and monitoring. The restrictions on travel and face-to-face working imposed the Coronavirus pandemic highlighted the benefits of remote commissioning to companies, many of whom are now looking to extract the most benefit from this technology.
HRS offers remote telemetry and control options for all applicable products and systems, using class-leading technology from Siemens and Allen-Bradley Products. We are keen to exploit the potential of process controls to improve levels of operational knowledge, process management and operational efficiency.
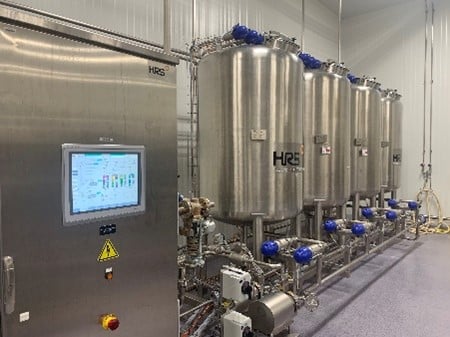
Process controls can incorporate a range of functions, such as visualization and Human Machine Interface (HMI) solutions, as well as programming tools and advanced software applications. We utilise a combination of programmable logic controllers (PLCs) and graphic terminals to provide easy to use, reliable controls.

HRS also utilises a suite of bespoke software to monitor and control key parameters. This data can easily be transferred to remote systems – either those belonging to the client or HRS itself, using either hardwired (ethernet) or secure wireless (4G/5G) communication technology.
Remote operation and monitoring provide a number of benefits, including the ability for clients to view and control equipment from a central point, something which is particularly beneficial for complex installations, or those which are spread across numerous buildings or sites. It also allows HRS staff to assist with operations such as commissioning, upgrading or running-in, and to provide ongoing technical support should this be required.
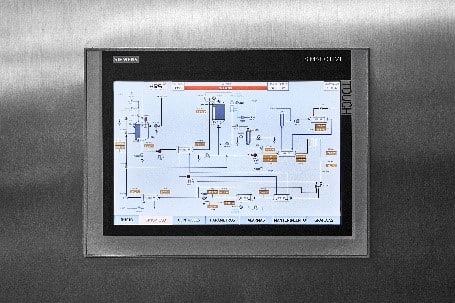
Looking to the future, digital process control technology is likely to become even more beneficial to processing industries. Control software can be constantly kept up to date, helping to keep systems operating at peak efficiency, but it is perhaps in the area of simulation that the greatest benefits could eventually be realised.
Engineers and commentators increasingly refer to the concept of a ‘digital twin’ – a virtual version of a physical system or piece of equipment which can be used to simulate any change to operation, from differences in product specification to adjusting physical settings such as valve diameter or tube length. When coupled with artificial intelligence (AI), such virtual systems can determine the optimum hygiene regimes, best energy efficiency and even the most productive time of day to run certain operations.
While our technology is not at this level yet, there is no doubt that as an industry we are getting closer. If such a future is to be realised, then information technology (IT) and operational engineering functions will need to become even closer, a trend which we are already seeing in many businesses. Industry 4.0 is a term that is often discussed, but not always fully appreciated. However, the last year has begun to show us what the near future will look like for process control.
About HRS Heat Exchangers
Located in the UK, HRS Heat Exchangers is part of the HRS Group which operates at the forefront of thermal technology, offering innovative heat transfer solutions worldwide across a diverse range of industries. With 40 years’ experience in a range of sectors, including food and drink, pharma, energy, water and industry. HRS specialises in the design and manufacture of an extensive range of turnkey systems and components, incorporating our corrugated tubular and scraped surface heat exchanger technology, HRS units are compliant with global design and industry standards. HRS has a network of offices throughout the world: Australia, New Zealand, UK, Spain, USA, Malaysia and India; with manufacturing plants in the UK, India and Spain.
For UK media enquiries about HRS Heat Exchangers please contact:
Yenni Maelianawati,, Senior Marketing Manager,
3 Abloy House, Hatters Lane, Watford, Hertfordshire, WD18 8AJ
Tel: +44 (0)1923 232 335l: email: yenni@uk.hrs-he.com
Email for publications: info@uk.hrs-he.com
www.hrs-heatexchangers.com