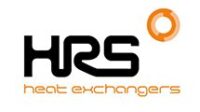
Member press release – Now is the time to maximise biogas
The current world political situation has highlighted the need to reduce our reliance on imported natural gas, and the key role that anaerobic digestion and biogas can play in these ambitions, as well as the importance of domestically produced organic biofertiliser in maintaining food production. On stand C107 at the World Biogas Expo 2022 in June, HRS Heat Exchangers will showcase its range of heat exchangers and bespoke systems to help plant operators and developers maximise AD plant production and efficiency.

HRS manufacture a range of heat exchangers for use in biogas production including the HRS Unicus Series of scraped surface heat exchangers for use in thermal hydrolysis to increase biogas production, the G Series for exhaust gas cooling and heat recapture, and the DTI Series for feedstock and digestate heating.

Our Biogas Dehumidification System (BDS Series) is specifically designed to removes water from biogas, protecting CHP engines from corrosion and cavitation. With heat recovery as standard to increase energy efficiency, the BDS reduces biogas temperatures from around 40 °C to approximately 5-7 °C, condensing more than 90 per cent of the water present via a chiller system, leaving a clean and dry biogas ideal for use in CHP engines.
As well as systems to improve biogas production, HRS also produces systems for the improvement and processing of digestate.

One of the most energy- and cost-efficient methods to pasteurise digestate is the HRS Digestate Pasteurisation System (DPS). The standard 3-tank DPS provides continuous pasteurisation, with one tank being pasteurised while one is filling, and another being emptied. The DPS uses a double tube heat exchanger to heat the digestate to 75 °C above the required pasteurisation temperature. This allows for variation in the sludge consistency and its incoming temperature, making sure that the digestate is always properly pasteurised. The tanks can also be used individually, for example to allow for routine maintenance.

The HRS Digestate Concentration System (DCS) uses patented technology to reduce the volume of the liquid fraction of digestate by up to 90%, raising the concentration of total solids to 20% solids while also maximising the nutrient content, using heat from the AD plant’s CHP engine.
Less water means reduced transport costs and field traffic, bringing further benefits in terms of reduced compaction caused by the application of the digestate to land. Another benefit of the DCS is odour and ammonia control, which helps increase the nutrient content of the digestate. The high temperatures and vacuum conditions needed to concentrate digestate can cause release of ammonia, largely responsible for the odours associated with digestate. The DCS overcomes this by acid-dosing the digestate with sulphuric acid, thereby decreasing the pH levels. This turns the ammonia into ammonium sulphate, which is not only less odorous, but is also an ideal crop nutrient.
To learn about the complete range of HRS solutions for biogas, visit stand C107 at The World Biogas Expo on 15-16 June 2022 at the NEC in Birmingham.
– ENDS –
About HRS Heat Exchangers
Located in the UK, HRS Heat Exchangers is part of the HRS Group which operates at the forefront of thermal technology, offering innovative heat transfer solutions worldwide across a diverse range of industries. With 40 years’ experience in the anaerobic digestion and biogas sector, specialising in the design and manufacture of an extensive range of turnkey systems and components, incorporating our corrugated tubular and scraped surface heat exchanger technology, HRS units are compliant with global design and industry standards. HRS has a network of offices throughout the world: Australia, Canada, New Zealand, UK, Spain, USA, Malaysia and India; with manufacturing plants in the UK, India, Spain and Canada.
For UK media enquiries about HRS Heat Exchangers please contact:
Yenni Maelianawati,
Senior Marketing Manager,
3 Abloy House, Hatters Lane,
Watford, Hertfordshire, WD18 8AJ
Tel: 01923 232 335
Direct Email: yenni@uk.hrs-he.com
Email for publications: info@uk.hrs-he.com
www.hrs-heatexchangers.com
Release issued by GloHouse Media:
Bev Small, email: bev.small@glohouse.co.uk, Tel: 01223 872239 / 07901 841491