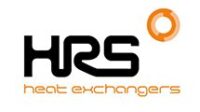
Member press release – HRS completes largest ever evaporator
At a manufacturing facility outside the Spanish town of Lorquí, a 16m high evaporator has steadily been constructed over the last 12 months. Now complete, the unit, which is the largest evaporation unit ever constructed by HRS Heat Exchangers, will soon be dismantled for transport and installation at its operating site.
The combined evaporator and crystalliser, which will have a total capacity of nine tonnes per hour once operational, has a footprint of 135 m2 and is designed to treat concentrated waste brine produced by an on-site reverse osmosis plant resulting in the production of distillate – which is returned as process water – and crystallised waste. This HRS evaporator unit will form part of an upgraded zero liquid discharge (ZLD) system for treating the client’s challenging waste stream and meeting local environmental regulations.
New HRS Evaporator System
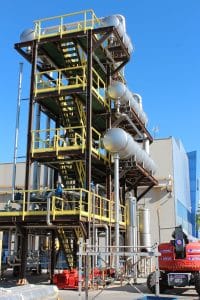
The new system has a total weight of 54 tonnes and covers a total area (across all four operating levels) of 420 m2. In total it includes 19 tanks, 15 heat exchangers of different sizes, and some 100 different lines of piping of various diameters. The system includes a pre-heater, degasser, evaporator and crystallisation sections, together with a final condenser.
In order to meet the challenging specification, including the highly corrosive nature of the sodium chloride-rich brine, which is produced by the client’s reverse osmosis system, the HRS system incorporates a number of non-standard features. Firstly, the heat exchangers have been constructed from titanium, rather than HRS’s standard construction materials of AISI 304 and AISI 316L stainless steel.
Secondly, rather than using a traditional five-effect forced recirculation evaporator, this system uses a five-stage multistage flash evaporator. The benefits of this flash evaporator over forced recirculation are that in only requires a single recirculation pump, instead of one pump for each effect, and that the pump is installed at the lowest temperature level in the loop, meaning less risk of cavitation and fewer issues with corrosion – a important consideration given the nature of the brine being handled. Finally, this design means that a lower overall recirculation rate is required, meaning less energy is required for the pumping process, improving overall process energy efficiency.
Once the brine has passed through the five-stage evaporator, the now concentrated brine is sent to a crystalliser unit, which removes the last of the distillate and produces 700 kg per hour of humid crystals (at approximately 70% dry matter).
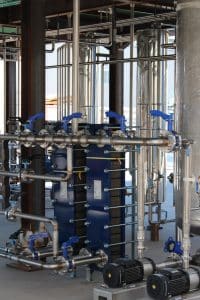
Once the crystals have been formed, the crystal ‘slurry’ is transferred to the client’s mechanical separator, where the humid crystals are extracted and any remaining saturated brine solution is returned to the crystalliser. As a result of this final crystallisation stage, no liquid from this process or waste stream will be discharged from the client’s site, making this a true ZLD effluent treatment solution.
Production, Installation and Commissioning
From winning the order in early 2022, it has taken 15 months for the multi-disciplinary HRS team, led by Technical Sales Engineer Tomas Stiebe, to design the evaporator and crystalliser and construct it at the manufacturing hub in Murcia. The unit is currently undergoing final checks and testing and will then be partially dismantled for delivery to the client. It is expected to be delivered to site in May and will then be commissioned by HRS engineering staff later in the year. Once fully operational it will process nine tonnes of brine effluent per hour, producing 700 kg of humid crystals and returning all distillate water to the existing client processes.
This system is the largest evaporator produced by HRS to date and builds on previous ZLD systems that the company has delivered to clients in Europe and further afield.
– ENDS –
About HRS Heat Exchangers
Located in the UK, HRS Heat Exchangers is part of the EIL Group (Exchanger Industries Limited) which operates at the forefront of thermal technology. HRS offers innovative heat transfer solutions worldwide across a diverse range of industries. With more than 40 years’ experience in the waste treatment and environmental sectors, specialising in the design and manufacture of an extensive range of turnkey systems and components, incorporating our corrugated tubular and scraped surface heat exchanger technology, HRS products are compliant with global design and industry standards. HRS has a network of offices throughout the world: Australia, Canada, New Zealand, UK, Spain, USA, Malaysia and India; with manufacturing plants in the UK, India, Spain and Canada.
For UK media enquiries about HRS Heat Exchangers please contact:
Yenni Maelianawati, Senior Marketing Manager, 3 Abloy House, Hatters Lane, Watford, Hertfordshire, WD18 8AJ
Tel: +44 (0) 1923 232 335
Direct Email: yenni@uk.hrs-he.com
Email for publication: info@uk.hrs-he.com
www.hrs-heatexchangers.com
Release issued for HRS Heat Exchangers by FastLoop Media:
Bev Small, FastLoop Media
T +44 (0) 7901 841491 E bev@fastloopmedia.com